Advocating the principles of “Learning by Doing”, Unitec is working closely with Pullman Learning Group to offer a range of cutting-edge simulation and emulation equipment in the new CIE building when it opens in 2017. Simulations and emulations are among the most frequently-used pedagogies across the automotive, welding and engineering industries, providing vital industry relevance and are a proven and powerful tool in engaging and retaining students in vocational areas.
The innovative equipment provides a simulated work environment allowing students to learn, experiment, troubleshoot and diagnose, all within a safe environment. For example, a virtual spray-painting booth will allow students to develop and improve techniques without being exposed to paint fumes.
A simulated automation laboratory will require programming of many of the same manufacturing and production subsystems found in industry today. An engine management trainer will introduce many common car faults which are diagnosed using industry specific tools and methodologies. And as new technologies are developed, they can be added to the range of equipment.
Pullman Learning Group GM David Birnbaum says, “The hands-on experience that simulation and emulation equipment provides students is critical to the acceleration of their learning speed and knowledge retention. Here students are making real-world connections using real componentry for real machines. The sensors you see on the automotive circuit boards are the exact same sensors you’ll see used in any top-line car or truck on the road.”
Unitec will also make the simulation and emulation suite available to wider community and industry groups for professional development and training.
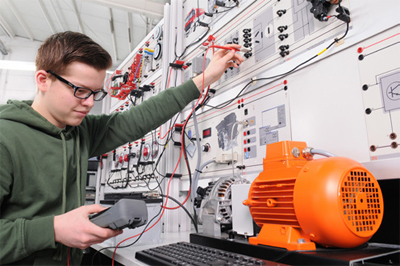